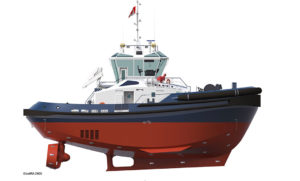
As electric ferries and tour boats become more common, the next big challenge is electric tugboats.
Two companies in particular have taken up that challenge: Crowley Maritime and Robert Allan Ltd. More stringent air pollution control regulations are driving interest in tugboats that run entirely on battery power.
In May, Robert Allan Ltd. announced five electric tugboat designs in its ElectRA series. All five will produce zero emissions during typical operations, but some will include backup diesel generators for firefighting and extended endurance.
In early July, Crowley announced it will build the first all-electric tug in the United States. Designed by Crowley Engineering Services, the 82-by-40-foot eWolf will deliver 70 tons of bollard pull with azimuthing drives, two 1,000-kW motors and 50 strings of batteries totaling 6.2 MWh.
“The tug represents everything Crowley stands for: innovation, sustainability and performance,” Tom Crowley, company CEO and chairman, said in prepared statement. The tug will operate at the Port of San Diego’s Tenth Avenue Marine Terminal and is projected to be in service by mid-2023.
The eWolf project arose through a public-private partnership between Crowley, the San Diego County Air Pollution Control District, the California Air Resources Board, the Port of San Diego, the U.S. Environmental Protection Agency (EPA) and the U.S. Maritime Administration.
The EPA provided $2 million toward the project through the Diesel Emissions Reduction Act, according to Kathleen Keehan, supervising air resources specialist for the San Diego County Air Pollution District. “It will be going to Crowley for building the e-tug,” she said. “The air district is providing an additional $8 million to Crowley for the e-tug through our Community Protection Program, and Crowley is making up the rest of the cost to build the new tug.”
The eWolf will be built by Master Boat builders in Coden, Alabama, with design and construction management provided by Crowley Engineering Services. The tug’s battery system will be charged by a shoreside station developed by Cochran Marine. A fully-integrated electrical package will be created by ABB Marine & Ports, along with artificial intelligence technology to increase safety and efficiency.
The future eWolf, which will generate zero carbon emissions during typical towing jobs, will replace a diesel-powered tug that burns 30,000 gallons of fuel annually. It also will sharply reduce particulate matter and other greenhouse gas emissions compared to a conventional diesel-powered tugboat.
It was Crowley that first contacted the Port of San Diego and asked them to become involved in the project, said Thom MacLean, director of energy and policy for the Port of San Diego. “They called me, and I said, ‘yes, we can do this.’ After that we began to solve the problems and try to figure out how to make it happen.” The port already has a clean air strategy, and this project fit within it.
In addition, MacLean said, innovative projects such as eWolf are crucial in the development of new propulsion technology. “Other companies, before they want to follow, want to see that it is working,” he said, “or at least have a good feel for it.”
Once completed, eWolf will be able to complete one or two ship-assist jobs on a single battery charge, depending on the specific job, according to Coulston van Gundy, a director of Crowley Engineering Services. Its projected 70 tons of bollard pull can be sustained for 30 minutes, he said.
The vessel’s design platform can be modified for other power needs and can also be built with hybrid propulsion, he said. The shore-side battery system can also be powered with solar panels, taking advantage of cheaper electric rates at different times of day. “We’ve designed it to charge at one megawatt per hour, so that crews can actually manage the size of the cables,” said van Gundy.
There is also the potential to use fuel cells to replenish the tugboat’s batteries through the shoreside charging station, he said. “This type of charging can be overridden to charge at a faster rate.”
The tug does have a small diesel generator for long trips. Its fuel capacity is between 10,000 and 15,000 gallons, depending on the tug design, which can be customized to meet the requirements of different operators.
Since there is no exhaust stack, the tug has 360-degree visibility from the helm station, so the operator can see aft without obstruction.
The design incorporates safety features such as reduced tripping hazards at the back of the pilot house, the insetting of some of the forward shoulder bits to prevent lines from hitting the crew and a built-in ladder on the side for self-rescue.
“We were basically able to build the vessel from the ground up,” said van Gundy.
Robert Allan Ltd.’s all-electric ElectRA series includes four tugs with various combinations of electric propulsion with back-up diesel generators. However, the ElectRA 2100 is fully electric. It is about 70 feet long and 36 feet wide, with a 15-foot draft. It has a maximum bollard pull of 50 tons.
Mike Phillips, product manager for Robert Allan Ltd., said one of the biggest challenges was figuring out how many batteries could fit in the vessel. “Undoubtedly, this is balancing range and endurance against capital costs that are proportional to the size of the battery pack,” he said.
“All but the [ElectRA] 2100 feature significant backup diesel generators, but these are still electric drive, with L-drive propellers,” Phillips said. The ElectRA 2100 not only eliminates backup diesel generators, “but many of the associated exhaust, ventilation, fuel and cooling systems as well,” he said. “This not only serves to reduce costs to a minimum, but also allows for even more space to be afforded in batteries.”
The ElectRA 2100, with a 5,160-kWh battery bank, can produce 50 tons of bollard pull for over an hour. “Practically speaking, of course, sustained operation at full bollard pull very rarely exceeds five to ten minutes, so the tug has ample endurance to complete missions on a single charge, including transit to and from the job site,” Phillips said.
It is possible to recharge the ElectRA 2100’s batteries in 15 minutes, but that would require a very large charging station. Most operators will choose smaller stations to recharge batteries in two-to-four hours, according to Phillips.
ABB also acknowledged the challenge around fitting sufficient battery power within a tugboat, which have significant power requirements and a limited machinery space. “This could create a challenge to fit electrical systems, including the batteries, into the hull design,” said Edward Schwarz, vice president for sales in ABB’s Americas division.
But without diesel propulsion, including the large engines that typically take up much of an engine room, he said there is flexibility to locate electrical equipment in different areas within the space.
“With the removal of large engines, shaft lines, gearboxes and fuel tanks,” he said, “it allows for the replacement with batteries.” •